Unlocking New Efficiency Levels: A Comprehensive Guide to Manufacturing Execution Systems (MES)
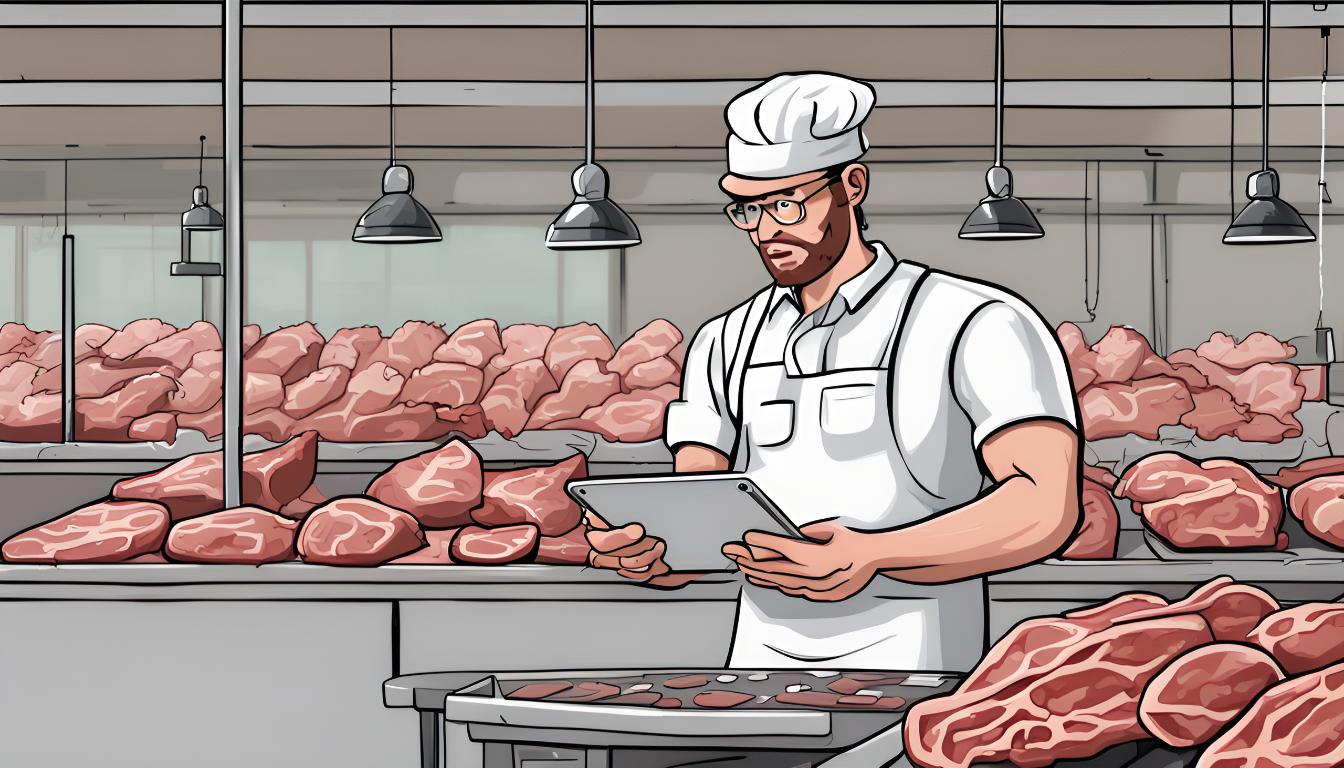
In the rapidly evolving world of manufacturing, an impressive 78% of companies report significant improvements in efficiency after implementing Manufacturing Execution Systems (MES). This statistic underlines the transformative power of MES in boosting companies' operational excellence. Understanding MES is crucial for manufacturers who want to increase productivity and remain competitive in today's market. MES software acts as a vital tool for managing production processes in real time, ensuring that manufacturers can respond quickly to market demands, optimize resources, and maintain quality standards.
Section 1: Understanding the MES Software
What is a MES Software:
Manufacturing Execution Systems (MES) are comprehensive software solutions designed to monitor and control manufacturing operations on the shop floor. These systems bridge the gap between enterprise resource planning (ERP) systems and the physical production process.
Main Functions:
The primary functions of the MES include:
- Real-time data management: Data capture and analysis of machines, processes, and operators.
- Process optimization: Streamlining workflows to increase productivity and reduce cycle times.
- Production planning: Ensuring the timely execution of production plans.
Importance:
MES is indispensable for competitive manufacturing, as it provides real-time information, allowing manufacturers to make informed decisions, optimize production, and improve overall efficiency.
Section 2: Key Benefits of MES
Increased Efficiency:
MES streamlines production processes by automating data collection and reporting, reducing manual errors and delays.
Improved Quality:
By ensuring compliance with established standards, MES reduces rework and waste rates, leading to higher quality products and customer satisfaction.
Increased Visibility:
MES offers transparency throughout the manufacturing process, allowing better monitoring of materials, production phases, and resource utilization.
Cost Reduction:
By optimizing resource allocation and reducing downtime, MES can significantly reduce operating costs, contributing to better profit margins.
Compliance and Traceability:
In regulated industries, such as pharmaceuticals and aerospace, MES plays a crucial role in ensuring compliance with industry standards and maintaining product traceability along the supply chain.
Section 3: MES in Different Industries
Food and Beverages:
In this sector, MES helps address unique challenges, such as maintaining food safety standards and managing complex supply chains. It ensures compliance with regulatory requirements, while optimizing production schedules to meet consumer demand.
Automotive and Aerospace:
MES automates supply chain management, allowing manufacturers to track parts and materials efficiently. In addition, it generates historical data, which are essential for quality assurance and continuous improvement.
Pharmaceuticals and Life Sciences:
In these highly regulated industries, MES standardises workflows and documentation, ensuring compliance with strict regulations and improving product safety.
Section 4: Challenges and Solutions in Implementing the MES
Complexity and Cost:
Implementing MES can be complex and costly, especially for small and medium-sized businesses (SMEs). However, these challenges can be mitigated through careful selecting the right implementation method and partner. Here is an overview of the main software implementation methodologies for factory shopfloors:
1. Waterfall Methodology
- Overview: The Waterfall method follows a linear and sequential approach, where each phase of the project must be completed before the next one begins. The phases typically include requirements gathering, system design, development, testing, deployment, and maintenance.
- Best For: Factories with well-defined processes and requirements where changes are unlikely once the project starts.
- Advantages:
- Easy to manage and monitor progress.
- Well-documented with clearly defined milestones.
- Drawbacks:
- Little flexibility; changes or new requirements introduced late in the project can be costly.
- Testing happens at the end, making it harder to identify issues earlier in the process.
2. Agile Methodology
- Overview: Agile is an iterative approach that emphasizes flexibility, collaboration, and incremental delivery of functional software. Instead of a full system roll-out, software is delivered in smaller, manageable chunks or "sprints" (typically 2-4 weeks).
- Best For: Factories that operate in dynamic environments where frequent changes or continuous improvements are necessary.
- Advantages:
- Greater flexibility to adjust to new requirements or changes.
- Continuous testing and feedback throughout the process.
- Faster delivery of functional parts of the system.
- Drawbacks:
- Less predictability in terms of overall timeline and scope.
- Requires high collaboration between teams, which can be challenging in some factory environments.
3. Hybrid (Waterfall + Agile) Methodology
- Overview: The Hybrid method combines elements of both Waterfall and Agile. It uses Waterfall for high-level planning and milestones but adopts Agile principles for the execution of phases, allowing for more flexibility during the development process.
- Best For: Factories that need structure but also require the flexibility to adapt as needed.
- Advantages:
- Structured with defined stages and milestones like Waterfall but adaptable during the execution like Agile.
- Balanced approach that can accommodate large, complex projects while still being flexible.
- Drawbacks:
- Can be challenging to manage due to the dual nature of planning and execution.
- Requires experienced teams to ensure that both methodologies are effectively blended.
4. Phased (Incremental) Rollout
- Overview: In this methodology, the software is implemented in phases across different parts of the factory or across different functionalities. For instance, one factory or department may go live first, followed by others.
- Best For: Large, complex factory environments where it’s risky or impractical to implement the system across the entire plant at once.
- Advantages:
- Lower risk due to gradual implementation.
- Easier to manage smaller rollouts and address issues before full implementation.
- Drawbacks:
- Slower overall implementation, which may delay full benefits.
- Different parts of the factory may be using different systems for a time, which can create operational inefficiencies.
5. Pilot Project Approach
- Overview: A pilot approach involves deploying the system in a small, controlled area of the factory first (such as a specific line or process), then reviewing and refining the solution before a broader rollout.
- Best For: Factories unsure about the software’s fit or those who want to test its impact before committing to a full implementation.
- Advantages:
- Reduces the risk of major disruptions since the system is tested on a smaller scale.
- Provides valuable insights into potential challenges before full deployment.
- Drawbacks:
- Slower process if used as the primary methodology.
- Additional cost and time may be required to make adjustments after the pilot phase.
6. Big Bang Implementation
- Overview: The Big Bang approach involves deploying the entire system across the whole factory in one go. All users and departments switch to the new system simultaneously on a predefined date.
- Best For: Factories with simpler, smaller operations where implementing the entire system at once is feasible.
- Advantages:
- Fastest approach to get the full system up and running.
- Avoids temporary inefficiencies of running multiple systems concurrently.
- Drawbacks:
- High risk due to potential for operational disruption.
- Limited time for user training and system testing.
7. Lean Implementation
- Overview: Lean methodology, adapted from Lean manufacturing principles, focuses on minimizing waste, improving efficiency, and delivering value quickly. It involves identifying key features and prioritizing them for early delivery, with continuous improvement afterward.
- Best For: Factories looking to reduce costs and improve efficiencies rapidly, often as part of a broader lean manufacturing strategy.
- Advantages:
- Fast delivery of the most valuable components.
- Focuses on efficiency and cost reduction.
- Drawbacks:
- Can result in an incomplete solution if not managed properly.
- Requires a cultural shift within the organization towards continuous improvement.
8. DevOps Methodology
- Overview: DevOps is a methodology that brings development and operations teams together to deliver and improve software in an automated, continuous manner. This is particularly suited to cloud-based systems where updates and improvements can be rolled out without disrupting operations.
- Best For: Factories adopting cloud-based solutions or those that want rapid, frequent updates to their software.
- Advantages:
- Faster, continuous deployment of new features and updates.
- High level of automation for processes such as testing, deployment, and monitoring.
- Drawbacks:
- Requires significant cultural and procedural changes to integrate development and operations teams.
- High level of technical expertise required for automation.
Section 5: Future Trends in MES
🚀 Technological Breakthroughs: The future of Manufacturing Execution Systems (MES) is nothing short of revolutionary! Emerging technologies like Artificial Intelligence (AI) and the Internet of Things (IoT) are transforming how MES operates, offering unmatched predictive analytics and boosting real-time decision-making. Imagine systems that not only respond but predict and solve problems before they happen—that's the power of AI and IoT!
📈 Market Explosion: MES is on the verge of explosive growth across multiple industries. As companies chase higher efficiency, flawless quality control, and data-driven decision-making, the demand for cutting-edge MES solutions will skyrocket. The future is all about smarter, faster, and more precise production—are you ready?
References
- Accenture (2020). Supply Chain Disruption. Retired from Accenture.
- BDO USES LLP. (2022). Middle-Market CFO Outlook Survey 2022. Retired from BDO Insights.
- TechTarget. Application Containerization. Retired from TechTarget.
- Cloud Native Computing Foundation. Kubernetes Certified Tools. Retired from CNCF.
- Synopsys. Definition of DevOps. Retired from Synopsys.
- Chen, T., & Voigt, K.I. (2020). Implementation of Manufacturing Execution Systems (MES) for Safety and Traceability.
- Shi, Y., et al. Identifying Food Safety Risks.