Stagnation Or Success? Advanced Planning and Programming (APS) on the Factory Floor as a Key Indicator of Operational Strength
Nowadays, food companies face increasingly complex challenges, making Advanced Planning and Programming (APS) an essential tool for optimizing operations and improving production efficiency along the supply chain.
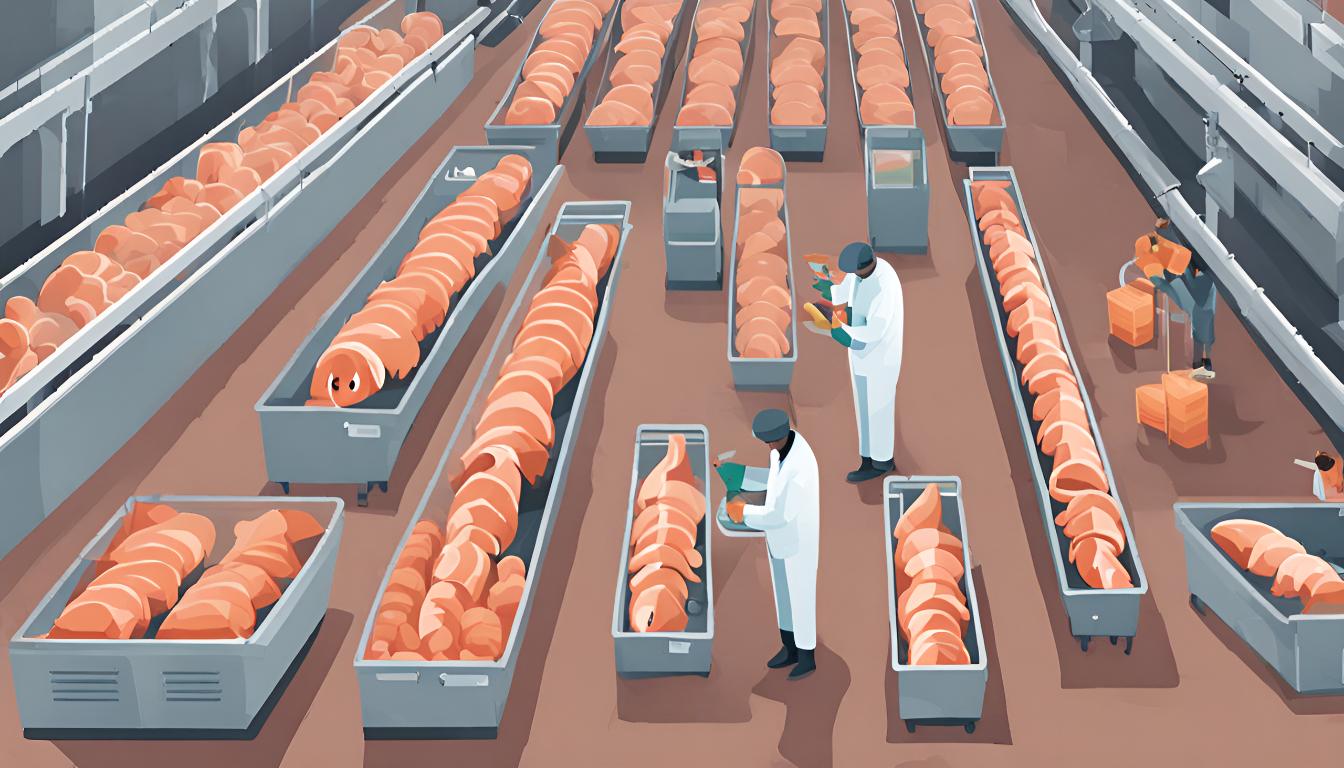
Nowadays, food companies face increasingly complex challenges, requiring efficient and innovative solutions. Advanced Planning and Scheduling (APS) emerges as a crucial tool for transforming production and optimizing operations in the food industry. By implementing APS systems, companies can not only reduce waste but also significantly improve operational efficiency. In this article, we will explore the power of APS systems in the meat, fish, and perishable food industries, highlighting success stories and the transformative impact of this technology.
What Is Advanced Planning and Programming (APS)?
Advanced Planning and Programming (APS) consists of a set of software tools that allow more efficient production management through resource optimization and accurate scheduling. Unlike traditional methods, APS systems provide real-time visibility into operations, allowing dynamic adjustments to respond quickly to changes in demand and availability of materials. These solutions are especially relevant for the food industry, where the perisability of products requires strict and efficient control of time and resources. In addition, APS systems enable better coordination between the different stages of production and logistics, contributing to a more integrated and efficient supply chain.
The Digital Transformation in the Food Industry
The digital transformation in the food industry has provided substantial improvements in operational efficiency and in the capacity to respond to market requirements. Advanced technologies such as APS systems play a central role in this revolution, allowing precise and integrated coordination between production, logistics, and distribution. The use of APS software provides real-time visibility of all operations, which facilitates informed and quick decision-making. In addition, these solutions help to predict fluctuations in demand and to adjust production as necessary, minimizing the risk of waste and overproduction. Companies such as Nestle And the General Mills have already benefited significantly from these technologies, demonstrating a reduction in waste and an increase in productivity. In the context of perishable foods, where time is a critical factor, digital transformation ensures that products reach the market in the best possible condition, preserving quality and freshness. By adopting these technologies, food companies are able not only to optimize their internal processes, but also to offer a better service to the final consumer, becoming more competitive in a globalized market.
Advantages of APS Systems in the Meat Industry
In the meat industry, the freshness and quality of the products are of the utmost importance. APS systems allow producers to quickly adjust production plans, ensuring that supply is always aligned with demand. This contributes to the reduction of raw material waste and to better inventory management, avoiding both scarcity and excess stock. In addition, the APS software facilitates the traceability of products along the supply chain, ensuring that all stages of production are monitored and optimized in real time. This ability to respond quickly is crucial to maintaining the quality and freshness standards required by consumers and industry regulations. The use of APS also improves operational efficiency by optimizing resource utilization and minimizing machine downtime, which translates into lower operating costs and greater productivity.
The Importance of APS in the Fish Industry
The fish industry, characterized by the high perisability of its products, benefits greatly from Advanced Planning and Programming (APS). With the ability to accurately forecast demand and adjust production accordingly, APS systems help minimize waste and ensure that products reach the market with the necessary freshness. These technological solutions allow efficient inventory management, avoiding both scarcity and excess stock, and facilitate the traceability of products along the entire supply chain. In addition, the implementation of APS systems optimizes logistics, ensuring that fish is processed and distributed effectively and in good time. The ability to make adjustments in real time according to variations in the supply of raw materials and market needs allows companies to maintain high quality and food safety standards, essential to satisfy consumers and comply with industry regulations.
Success Cases: Examples of Implementing APS Systems
Several companies in the food industry have demonstrated notable success with the adoption of APS systems. A Nestle, for example, was able to optimize its global supply chain, reducing raw material waste and improving on-time delivery by more than 12%. Another example is the General Mills, which, by integrating APS systems, reduced production cycle time by 20%, adjusting production in real time and improving order accuracy. Already the PepsiCo reported a 30% increase in productivity and a 15% reduction in operating costs, thanks to better resource management and the minimization of downtime. These cases highlight how APS systems can transform operational efficiency and resource management in the food industry, resulting in significant gains in both productivity and cost reduction.
How to Choose the Right APS System for Your Factory
Choosing the right APS system for your plant involves a careful assessment of several critical factors. First, it is essential to understand the specific needs of your operation, including the volume of production, the complexity of the processes, and the long-term goals. An APS system must be flexible enough to adapt to the particularities of your business and robust enough to handle fluctuations in demand and supply.
Another important aspect is the ability to integrate the APS system with existing systems in your factory, such as ERP (Enterprise Resource Planning). The smooth integration between different platforms guarantees coordinated and efficient management, facilitating visibility and control at all stages of production. Choosing a vendor that offers efficient and ongoing technical support is equally crucial, ensuring that the implementation and maintenance of the system are carried out smoothly.
Also, consider the cost-benefit of the solution. While the initial investment may be significant, gains in efficiency, reduced waste, and increased productivity must be weighed. The scalability of the system is also a factor to take into account; the APS system must grow with its operation, accommodating new challenges and future expansions.
Finally, look for references and case studies from other companies in the food sector that have successfully implemented APS systems. These practical examples can provide valuable insights and help you make a more informed decision.
The Future of Advanced Planning and Programming
The continuous evolution of digital technologies predicts a promising future for Advanced Planning and Programming (APS) in the food industry. The integration with artificial intelligence (AI) and machine learning will allow even more accurate forecasts and adjustments in real time, boosting the capacity to respond to fluctuations in demand and supply. In addition, the connectivity provided by the Internet of Things (IoT) will allow constant and detailed monitoring of all production processes, from the raw material to the final product. This interconnectivity will facilitate the automation of repetitive tasks and the continuous optimization of operations. Advanced data analysis will also be a crucial component, allowing companies to identify patterns and trends that can influence strategic decisions. As blockchain technologies become more prevalent, traceability and transparency along the supply chain will be significantly improved, ensuring compliance with regulations and consumer trust. Companies that invest in advanced APS systems will be better equipped to innovate, reduce costs, and improve sustainability, while remaining competitive in an ever-changing global market.
How BRAINR + Industrial ERP Can Help You “Seriously”
BRAINR + industrial ERP solutions stand out for offering deep and efficient integration between different aspects of production, essential for the successful implementation of APS systems. With BRAINR, companies are able to centralize data management, obtaining complete and real-time visibility of operations, from the acquisition of raw materials to the distribution of final products. This level of integration allows dynamic and informed adjustments, essential to optimize production and reduce waste.
The ability to customize these tools means that they can be adapted to the specific needs of each company, regardless of its size or complexity of the processes. In addition, integration with ERP facilitates the coordination of business resources, ensuring that all operations are aligned and that decisions are made based on accurate and up-to-date data.
Another strong point of BRAINR + ERP Cocacionado is its intuitive interface, which simplifies the adoption and use of the system by employees. Training and ongoing support ensure that the team is always prepared to maximize the benefits of APS technology. With these solutions, food companies can not only improve operational efficiency and inventory management, but also increase their capacity to respond to market changes, guaranteeing high quality and fresh products for consumers.