Industry 4.0, MES, and Food Production: Frustrated Love Triangle or Still in the Beginning of Dating?
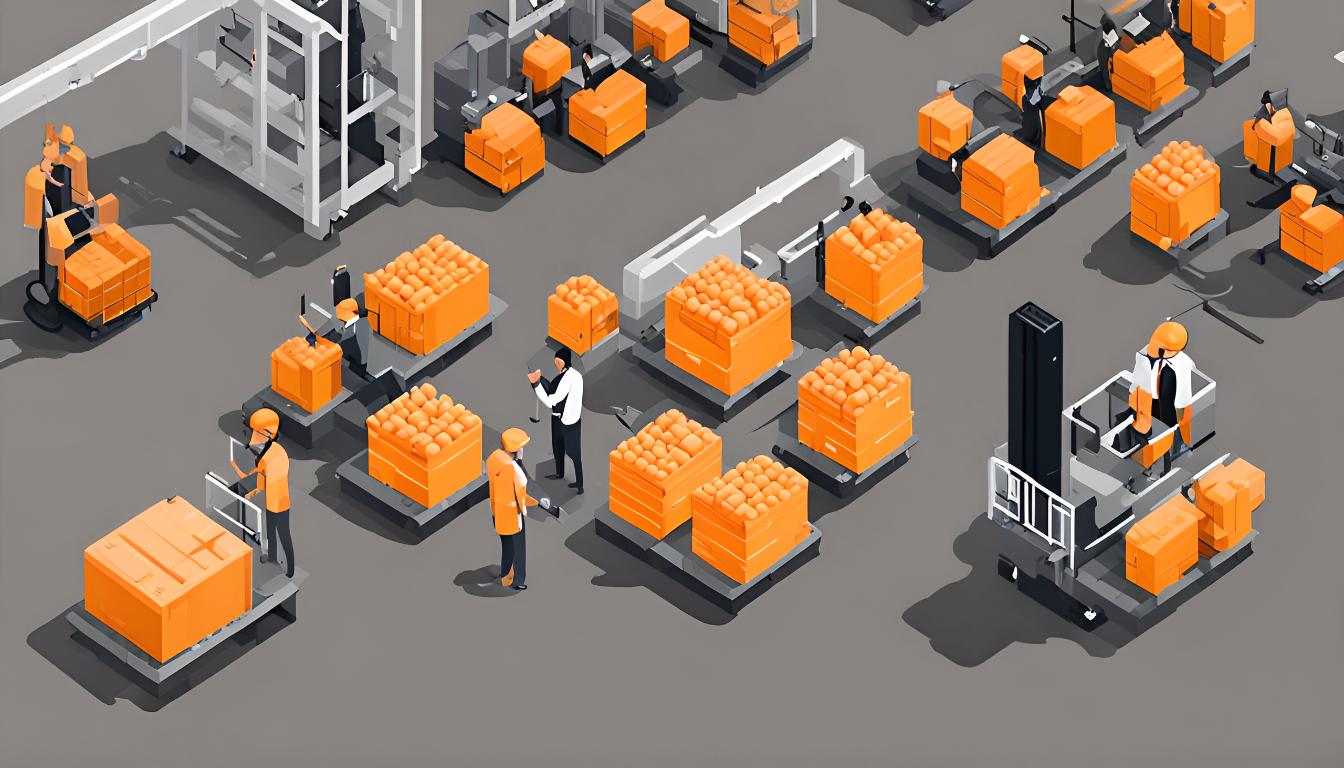
In the era of Industry 4.0, digital transformation has become a fundamental pillar for the evolution of industrial sectors, including the food industry. The Manufacturing Execution System (MES) emerges as an essential tool that revolutionizes the way food production is managed. With the integration of MES into industrial ERP systems, such as SAP, SAGE, PHC or springtime, companies are able to optimize processes, improve product quality, and increase operational efficiency.
Benefits of Implementing MES in the Food Industry
Implementing MES software brings a variety of significant benefits to the food industry. First, it improves visibility and control over the entire production process, from the raw material to the final product. This allows for more efficient management of resources and a reduction in waste. In addition, MES enables the automation of repetitive tasks, thus freeing employees to more strategic functions.
Another important benefit is the ability to ensure compliance with food safety and quality standards. The MES monitors processes in real time, ensuring that all critical parameters are strictly followed. MES and ERP integration offers a comprehensive view that improves decision-making and allows for quick adjustments in response to market changes or regulations.
Additionally, the use of an MES system can contribute to the optimization of the supply chain. With accurate and up-to-date data, companies are able to predict future needs and adjust their operations proactively, thus reducing the risk of stock disruptions and excess inventory. The MES also facilitates predictive maintenance of equipment, preventing breakdowns and increasing their longevity.
The flexibility provided by MES allows companies to adapt quickly to new products or changes in production, without the need for significant investments in new infrastructure. This ability to adapt is crucial in a market as dynamic as the food industry, where innovation and quick response to consumer trends are key factors for success.
Additionally, MES offers traceability capabilities that are essential for food safety. In the event of a need for a recall, the company can quickly identify and isolate the affected lots, minimizing negative impacts on the organization's reputation and finances. With an MES system, transparency is maximized, promoting the trust of consumers and business partners.
MES software, when integrated with ERP systems, offers a complete solution that promotes efficiency, compliance, and continuous innovation in the food industry.
Challenges Faced in Implementing MES
While implementing an MES system offers numerous benefits, it's important to recognize the challenges that may arise during the process. One of the main obstacles is resistance to change within organizations. Implementing new technologies involves altering established processes and, often, this is met with resistance from employees. To mitigate this challenge, it is essential to invest in training and awareness, promoting a culture of acceptance and adaptation to new tools.
Another significant challenge is the technical complexity involved in integrating MES with existing systems, such as ERP. This integration is crucial to ensure that data flows smoothly between different systems, allowing for a unified view of operations. However, the lack of compatibility between software and the need for customizations can complicate the process. The choice of experienced technological partners and detailed planning are essential to overcome these barriers.
Additionally, the initial implementation cost can be high, representing a significant investment for many companies. This cost not only comes down to the acquisition of the software, but also involves the necessary infrastructure, personnel training, and possible temporary interruptions in production during the transition phase. To face this challenge, companies must carry out a detailed cost-benefit analysis, considering long-term efficiency and productivity gains.
Finally, data security is a growing concern in the digital age. Implementing an MES system exposes operations to potential cyber threats, requiring robust IT security measures. Companies need to ensure that their MES system is protected against attacks, adopting advanced cybersecurity practices and constantly updating their defenses against new threats.
MES Implementation Success Stories
Numerous food companies have reaped the benefits of implementing industrial MES software. A successful example is Nestlé, which was able to increase the efficiency of its factories around the world through MES automation. The company reported a significant reduction in downtimes and an increase in product quality.
Another notable case is that of Danone, which implemented an MES system to improve the traceability of its products. With the new system, the company is able to monitor each production batch, from the origin of the ingredients to the delivery of the final product. This detailed tracking capability helps ensure food safety and protects the brand.
A third successful example is Ferrero, known for its confectionery products. Ferrero adopted an MES system to optimize its production line, resulting in greater flexibility and responsiveness to changes in market demand. The company was able to reduce production cycle time and increase productivity, while maintaining high quality standards.
In addition, Unilever also benefited from the implementation of an MES system. The company was able to integrate MES with its existing ERP system, allowing for a more cohesive and effective management of its production processes. Unilever reported significant improvements in product consistency and resource utilization, resulting in a more sustainable operation.
Finally, Mondelez International used an MES system to centralize the management of its global operations. This system allowed better coordination between factories around the world, promoting the standardization of processes and the sharing of best practices. With the implementation of MES, Mondelez was able to achieve greater uniformity in the quality of its products, regardless of the production location.
Main MES/MOM Software Players for the Food Industry
The MES/MOM software market for the food industry is highly competitive, with several companies that stand out for their offer of innovative and effective solutions. Siemens, through its software SIMATIC IT, is one of the most recognized names, providing robust integration with ERP systems and solutions that promote the efficiency and quality of production processes.
Rockwell Automation is another significant player in the market, with its platform FactoryTalk which ranges from production to logistics, facilitating end-to-end MES automation. This platform is known for its customization capacity and for the ease of integration with pre-existing systems, offering a high degree of flexibility.
A Schneider Electric it also stands out with its range of MES/MOM solutions that are adapted to the specific needs of the food industry. The company offers tools that help improve operational efficiency and compliance with food safety regulations, allowing for more effective management of resources and processes.
Honeywell is another important name in the sector, with MES/MOM solutions that focus on optimizing production and improving product quality. Its tools are known for their robustness and integration capacity, providing a complete and detailed view of manufacturing operations.
Additionally, companies such as ABB and GE Digital also have a significant presence in the market, offering solutions that combine industrial automation with advanced MES functionalities. These solutions help food companies to optimize their production processes and to ensure product traceability and quality.
With a wide range of options available, food industry companies have at their disposal a variety of MES/MOM solutions to meet their specific needs and promote the digital transformation of their production processes.
BRAINR as a Cloud-Native MES Leader for the Food Industry
BRAINR stands out in the cloud native MES scenario for its innovative and adaptable approach, specially designed for the food industry. Unlike traditional solutions, BRAINR offers a platform that allows automatic updates and real-time access to production data, regardless of location. This is crucial for food companies that require agility and quick response to market changes.
One of the main benefits of the BRAINR MES solution is the ease of integration with ERP systems, such as SAP, promoting a cohesive and efficient management of production processes. The cloud native platform eliminates the need for heavy investments in local infrastructure, allowing for faster and less expensive implementation.
BRAINR's flexibility allows companies to quickly adjust their production processes to new regulatory requirements or standards, something fundamental in a sector as dynamic as the food sector. In addition, data security is a priority for BRAINR, which implements robust cybersecurity measures to protect operations against potential threats.
Another significant advantage is the scalability of the solution, which allows companies to grow and expand their operations without facing technological limitations. The traceability capacity offered by BRAINR is essential for compliance with food safety regulations, allowing detailed monitoring of each stage of the production process.
In short, BRAINR offers a cloud-native MES solution that not only improves operational efficiency, but also guarantees compliance and quality of food products. This innovative approach positions BRAINR as a leader in providing MES solutions for the food industry, helping companies to remain competitive in the era of Industry 4.0.